お役立ちコラムCOLUMN
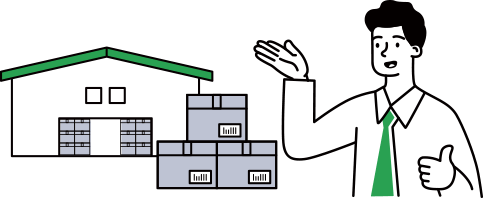
倉庫作業におけるロケーション管理を改善する8つのポイントとは
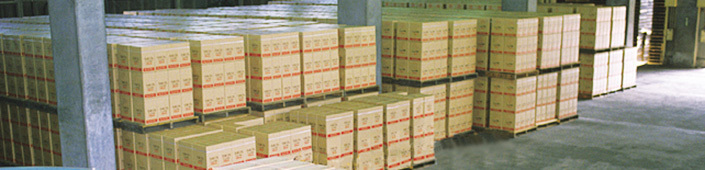
倉庫管理においてロケーションの管理方法を改善することで、作業の効率化やミスの防止など様々なメリットを得ることができるようになります。
ここではロケーション管理を改善する際に気を付けるべき8つのポイントをご紹介します。
間口サイズの最適化
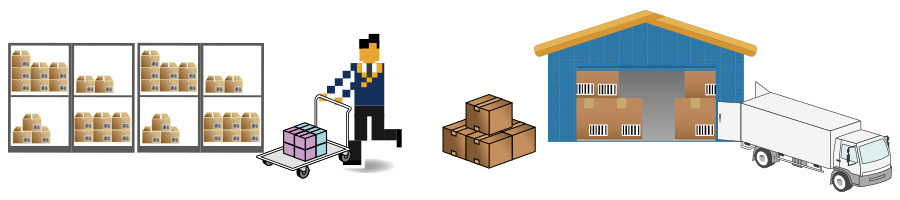
商品を保管する棚の間口のサイズは、商品・通箱などの大きさと保管する数量、必要な間口数などを考慮し適切な大きさにする必要があります。
間口のサイズを決め、各間口に一定のルールで、誰でも理解しやすい、分かりやすい番号を振ることがロケーション管理を改善する第一ステップになります。
適切なロケーション管理方法の検討
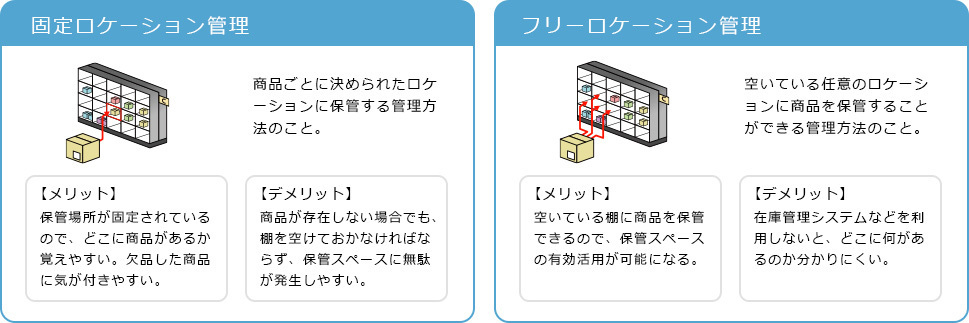
ロケーション管理には大きく分けて商品の入庫する棚が事前に決まっている固定ロケーションと任意の棚に商品の入庫が可能なフリーロケーションがあります。
固定ロケーションのメリットとして、商品が欠品した際にその商品の棚が空くのですぐに欠品に気づくことができる点や作業する方が商品の棚の場所を覚えることができるので、慣れた方であればスムーズに作業ができる点などがあります。
また、フリーロケーションのメリットとしては、商品が欠品している場合にはその商品のための棚を空けておく必要がないので、棚の有効活用が可能である点などがあります。
補充作業を考慮した保管場所の最適化
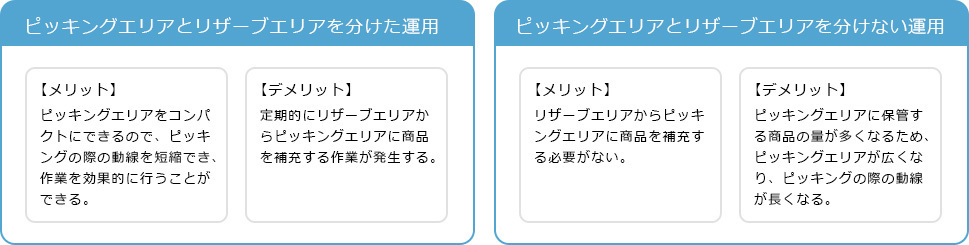
商品をピッキングするためのエリア「ピッキングエリア」とそのピッキングエリアに商品を補充できるよう商品をストックしておく「リザーブエリア」を分けておくことで、ピッキングエリアをコンパクトにする事ができ、動線を短縮。作業効率を上げることができます。
しかし、頻繁に補充しなければならない商品や商品自体が重く移動が困難な場合には、ピッキング用の商品と補充用の商品をまとめて保管した方が効果的なケースもあります。
商品と運用の特徴を理解し、ピッキングエリアとリザーブエリアの配置を決める必要があります。
出荷頻度が高い商品を作業開始位置や出荷口付近に保管
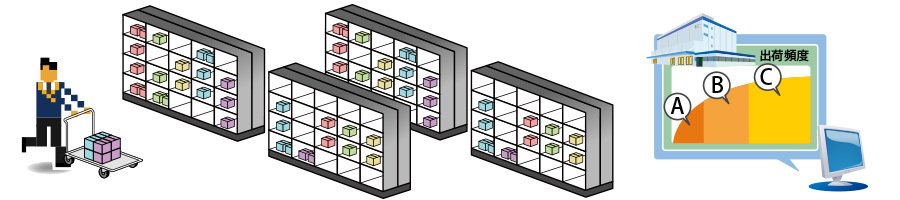
出荷ABC分析を行うことで、商品の出荷頻度が簡単に確認できるようになります。
出荷頻度の高い商品を作業開始位置や出荷口付近に配置することで、作業動線の短縮が実現し、作業効率を改善できるようになります。
また、その際には作業する方が1ヶ所に集中し渋滞が発生しないよう、作業動線を意識したロケーションの配置をする必要があります。
一緒に出荷される商品を近くに配置
ロケーション管理を行う際に、在庫管理システムを導入。バーコードとハンディターミナルなどを利用することで、効果的に業務を行えるようになります。
手書きで管理する手法に比べ、素早く行えるようになり、ロケーション管理の精度も向上します。
ピッキングミスを防止できるよう類似商品を離して保管
類似商品が近くの棚に保管してあるとどうしてもピッキングミスが生じてしまい、結果誤出荷に繋がってしまうということは少なくありません。
類似商品を離して保管することで、ピッキングミスを減らすことも可能になります。
不良在庫の適切な管理
売れる見込みのない不良在庫が多数存在し、それらの商品ごと間口に保管されていると、保管スペースの有効活用は難しいのではないでしょうか?
売れる見込みのない不良在庫をまとめて一ヶ所に保管することで、保管スペースを有効活用できるようになります。
在庫管理システムとハンディターミナルなどの導入
ロケーション管理を行う際に、在庫管理システムを導入。バーコードとハンディターミナルなどを利用することで、効果的に業務を行えるようになります。
手書きで管理する手法に比べ、素早く行えるようになり、ロケーション管理の精度も向上します。
まとめ
適切なロケーション管理方法の選択や、商品の保管場所の最適化を行うことで、倉庫内作業の効率化が実現します。
この機会にロケーション管理の改善を検討してみてはいかがでしょうか?